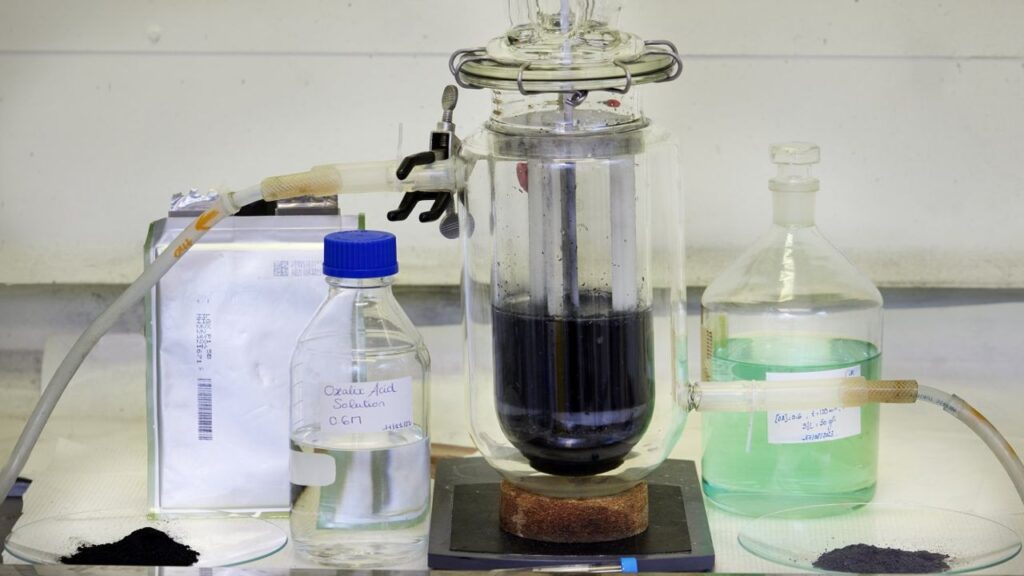
Recycling electric car batteries
Recycling electric car batteries – Swedish engineers believe they have finally found a solution for recycling electric car batteries. Although the carbon footprint of these vehicles is much smaller than that of combustion vehicles, battery recycling is still an unsolved problem, representing a significant environmental liability for the electrification of transport.
The new method allows the recovery of 100% of aluminum and 98% of lithium in electric car batteries. At the same time, the loss of valuable raw materials such as nickel, cobalt, and manganese is minimized. No expensive or harmful chemicals are needed in the process because the researchers used oxalic acid, an organic acid that can be found in the plant kingdom.
The water-based recycling method is called hydrometallurgy. In traditional hydrometallurgy, all the metals in an automotive battery are dissolved in an inorganic acid, which then collects metals such as aluminum and copper. Finally, cobalt, nickel, manganese, and lithium are recovered separately. Although the amount of residual aluminum and copper is small, several purification steps are required and each step in this process can cause lithium loss.
With the new method, the researchers reversed the order, recovering lithium and aluminum first. This way, it is possible to reduce the waste of valuable metals needed to manufacture new batteries, which are lost through conventional methods.
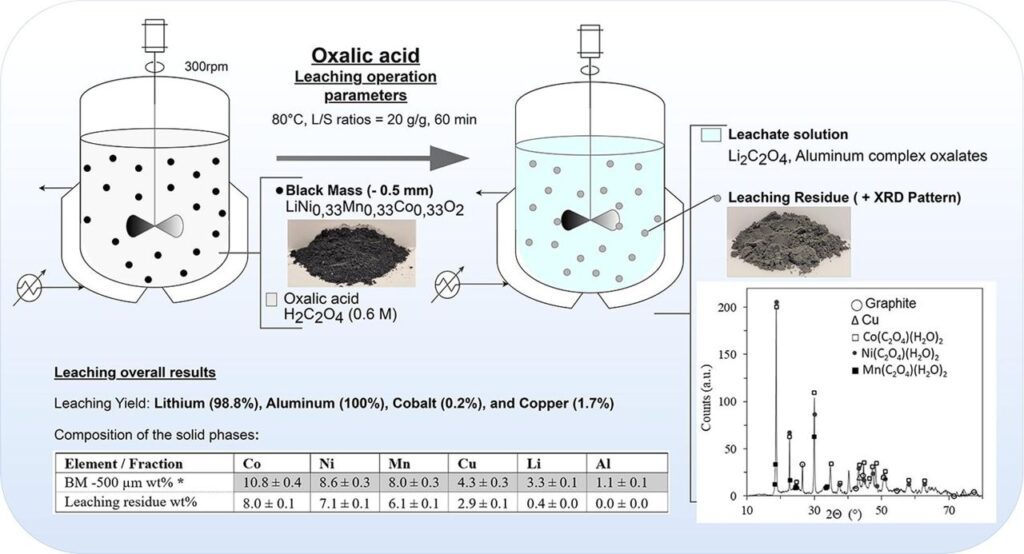
Battery hydrometallurgy
It all starts by pulverizing the contents of the battery, generating a very fine dark powder that is dissolved in the oxalic oxide. It seems simple, but the process involves careful control of temperature, concentration, and time. Finally, the mixture is filtered, leaving something similar to coffee grounds remaining – the aluminum and lithium remain in the liquid and the other metals remain in the solid part.
The next stage of the process is then missing, which consists of separating the aluminum and lithium, but the team claims that this will not be a problem. “Because the metals have very different properties, we don’t think it will be difficult to separate them. Our method is a promising new route for battery recycling – a route that deserves further exploration,” said Rouquette.