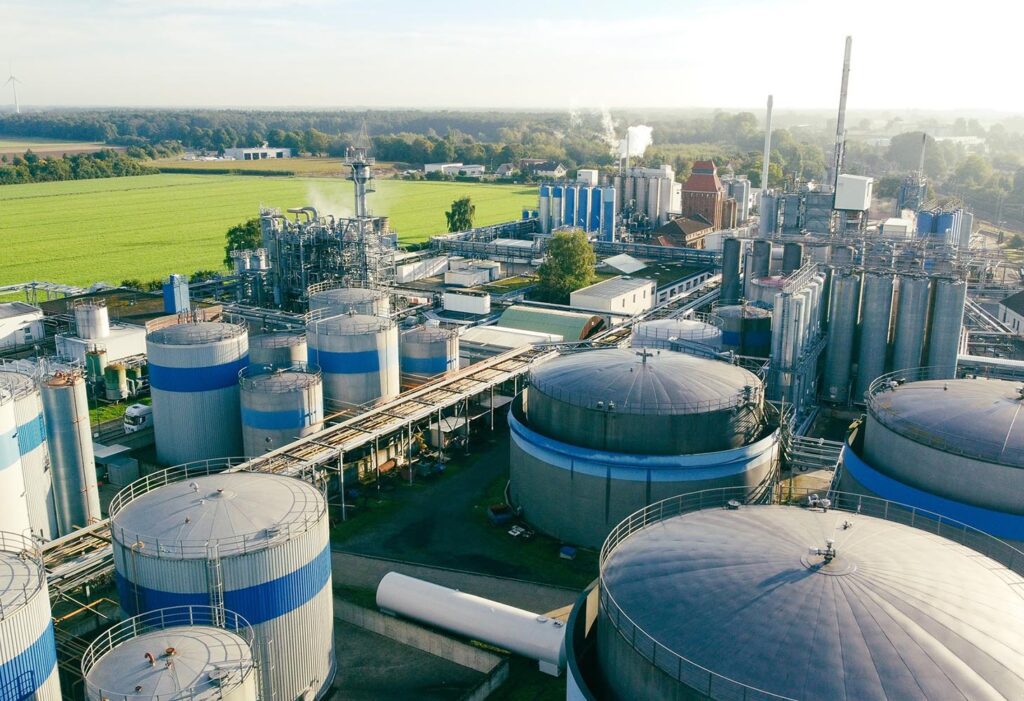
Re-refined base oils
Re-refined base oils – Interest in re-refined base oils (RRBOs) is growing alongside the trends of recycling, reducing carbon footprints and a desire to protect the environment. Rather than disposing of waste oils, an increasing number of producers are collecting used oils and removing impurities through technological processes such as vacuum distillation, hydrotreating, clay treatment, and solvent extraction.

In the past, the quality of RRBOs has proven a barrier to wider adoption. Early RRBOs developed a second-rate reputation, with observable colour differences and a sometimes-noticeable odour. Improvements in collection practices, infrastructure, better feedstocks—from the transition to higher-quality base oils—and more advanced re-refining technologies now support a much higher quality product.
Contrasting rates of oil collection and regeneration are prevalent around the globe. Many countries do not have re-refineries and even those that do face ongoing challenges. A significant share of RRBOs is currently Group I—which is produced by solvent refining—a declining market. Covid-19 also hurt the practice of re-refining, severely interrupting the collection of used oil.
Despite these constraints, the volume of used oil collected and re-refined is expanding. Increasing regulations around circularity are shaping the industry. Many analysts expect this upwards trajectory to continue. A recent report valued the global RRBO market at USD6.4 billion in 2021, with projections that it will reach USD8.8 billion by 2027, at a compound annual growth rate (CAGR) of 6.5%. Asia-Pacific is expected to be the fastest-growing market for RRBO in the forecast period.
As climate change reaches a crescendo, lubricant producers are realising their objectives can be achieved using circular solutions that allow carbon to be used again and again. The environmental footprint of products using RRBO is lower than conventional lubricants produced from virgin base oils, says Aimilia Neroutsou, product manager at TotalEnergies. Carbon dioxide (CO2) emissions are reduced by 20% to 40% compared to the original product, she says. The process also resolves issues around the disposal of spent lubricants.
Neroutsou and Jochen Hörer, of Bosch Rexroth, delivered a combined presentation on Re-Refined-Base-Oils (RRBO) – A first step to CO2 reduction and circular economy in hydraulic fluids during the 1st International Conference on Tribology and Sustainable Lubrication, held in Düsseldorf, Germany from April 18-19, 2023.
During the presentation, Hörer stressed the need for RRBOs to demonstrate equivalent performance in the field to totally substitute virgin base stocks. Not only do RRBOs require interchangeability with conventional Group I, II and III base stocks, but manufacturers also need to adopt eco-design principles for re-refined products. However, Hörer noted a lack of research data on the differences between mineral oil and RRBOs.
Neroutsou highlighted the importance of breaking the traditional linear model of manufacturing lubricating oils from virgin and fossil raw materials and the continuous and endless waste generation. A circular concept to produce lubricating oils has positive impacts on raw material supply—with the promotion of local raw materials, and reduces CO2 generation, she says.
The TotalEnergies representative outlined some of the current trends and regulations driving greater circularity including obligations to re-refine a certain percentage of base oils. Europe’s Green Deal, a set of policy initiatives with the overarching aim of making the European Union climate neutral in 2050, was launched in 2019. The legislation includes the Circular Economy Action Plan that incorporates a Sustainable Products Policy to enable greater circularity in industry. The policy mandates the inclusion of greater recycled content in products and the reduction of carbon and environmental footprints.
Similar commitments are emerging around the world. In December 2020, Turkey enacted regulation related to the management of used oils that includes collection targets and mandatory recycling into lubricants. In 2022, China updated regulations T/CNRRA 0901 and national standard GB/T 17145. Local regulations require all waste oil to be collected and treated by licensed companies. In May 2023, India’s Ministry of Environment, Forest, and Climate published a notification expanding its Extended Producer Responsibility (EPR) Scheme to used oil. Implementation date is proposed to start in April 2024, which will require 10% of base oil or lubricants sold or imported to be from re-refined base oil. The RRBO component increases yearly up to 60% by 2029.
Neroutsou and Hörer’s presentation outlined a development approach for hydraulic fluids formulated with RRBO to ensure “non-compromising” performance. Base stock covers around 99% of hydraulic fluids. The quality of hydraulic fluids is critical to the reliable operation of hydraulic drives and must be selected carefully for individual applications. In recent years, demands on hydraulic fluids have increased significantly alongside a rise in power-to-weight ratios.
TotalEnergies has adopted an eco-design approach for the formulation of high-performing hydraulic fluids using RRBOs. The journey begins with the careful selection of sustainable, non-hazardous raw materials for formulating with RRBO, says Neroutsou.
An in-depth evaluation of hydraulic fluids containing RRBOs is critical to achieving maximum performance. Enormous differences exist between hydraulic fluids that are available on the market, despite exceeding minimum standards. The minimum requirements specified by the German Institute for Standardisation (DIN) and the International Organisation for Standardization (ISO) are not sufficient to ensure quality, says Hörer. They do not allow for differentiation between the fluids or account for the chemicals used by lubricant manufacturers.
Bosch Rexroth has developed an independent performance standard that tests hydraulic fluids at high loads over several hundred operating hours. Hydraulic fluids that meet the requirements of Bosch Rexroth RDE 90235 conform with the minimum requirements of DIN 51524 part 2/3, ISO 15380, and ISO 12922, as defined in the Bosch Rexroth component data sheets.
However, Hörer outlined additional testing requirements to receive a favourable rating by Bosch Rexroth AG. RDE 90235 includes a review of manufacturers’ data from ISO 11158, ISO 15380, and ISO 12922. The technical characteristic values of the hydraulic fluid are extended by the Bosch Rexroth standard. Alongside stricter standard characteristic values, RDE 90325 also includes motor and pump tests as well as a specified, static seal test, which are assessed against defined components and conditions.
The most important aspects of the testing requirements are the in-house tests, says Hörer.
The pump test assesses fluid under realistic maximum conditions over 510 hours. A 10-hour run-in is completed before a 300-hour swivel test at 450 bar and 4000 rpm, followed by 200 hour corner power test at 500 bar and 4000 rpm. To ensure no problems with swelling or hardening of components, the new static Seal Test 802-1 is performed over 1008 hours. Hörer noted that retention samples of base stocks and finished oils are tested and stored for future reference.
Bosch Rexroth procedures are amongst the toughest in the market. RRBO and mineral-based hydraulic fluids are both subject to this thorough quality assessment. However, Hörer outlined additional requirements for RRBOs, including detailed screening to ensure the same health, safety and environment requirements are comparable to mineral oils. Realistically, you cannot see the difference between mineral oils and RRBO, says Hörer.
On successfully passing the RDE 90235 testing, a hydraulic fluid is included in the Bosch Rexroth Fluid Rating List 90245 which accompanies the issuance of a quality label to instantly identify the performance of the hydraulic fluid.