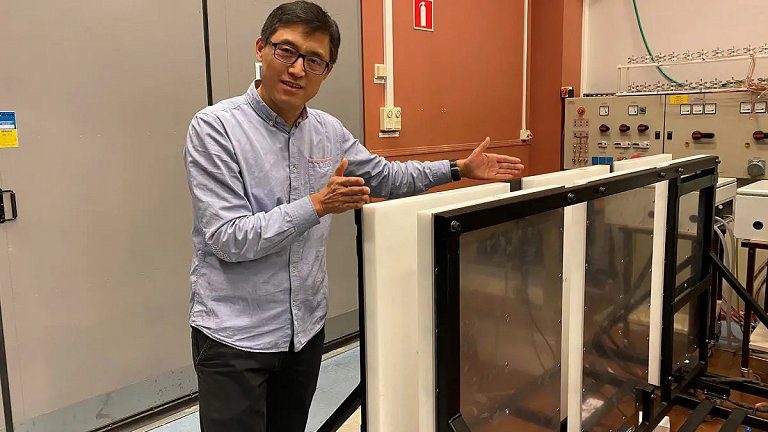
Wireless battery charging
Wireless battery charging – An emerging type of semiconductor made from silicon carbide and a new method of manufacturing and assembling traditional copper wires. These are the factors that are making the transmission of electricity through the air at high power, necessary to recharge large electric vehicles.
The combination of the two techniques has just been demonstrated by Professor Yujing Liu, from Chalmers University of Technology, in Sweden.
Although the inductive recharging – without the need for plugs – of the batteries of the electric cars is already being tested in several places in the world, the thing is much more complicated when we talk about public transport, from buses and trains to ferries, or even vehicles that operate in agriculture or mining.
In such cases, to be practical, inductive recharging must be fast and high power.
“You could have a system built into the pier that loads a ferry at the same time as passengers board and disembark. Automatic and completely independent of weather and wind, loading can happen 30 to 40 times a day. That’s probably the most obvious application,” exemplifies Professor Liu.
“Previous systems for wireless charging of vehicles used frequencies of around 20 kHz, much like a normal stove. They became bulky and transferring energy wasn’t very efficient. Now we’re working with frequencies four times higher. Then all of a sudden , the induction becomes attractive,” Liu contextualized.
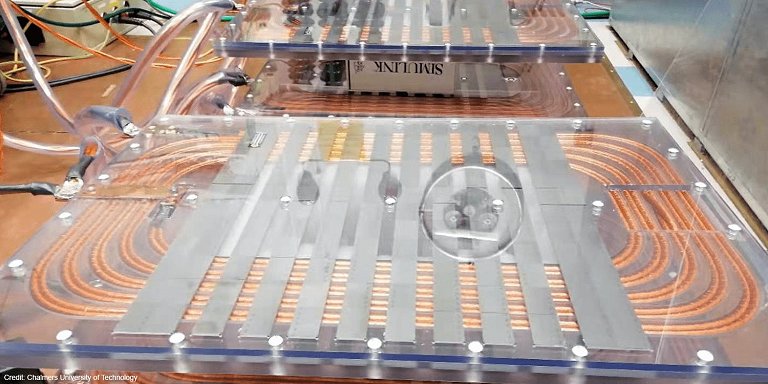
Whether on ferries or big trucks, it’s all about power: Try recharging these batteries the plug-in method and you’ll soon find that the power cords have to be so thick that everything becomes impractical. In fact, some pioneering experiments had to use industrial robotic arms to handle these cables.
That’s where the two technologies come in, which are making it possible to dispense with all this hassle.
“A key factor is that we now have access to high-power semiconductors based on silicon carbide, so-called SiC components. As power electronics products, they have only been on the market for a few years. They allow us to use higher voltages, higher temperature, and much higher switching frequency, in comparison with classic silicon-based components,” says the researcher.
While wireless car chargers typically operate at frequencies around 20 kHz, SiC electronics are allowing closer to 100 kHz. This is important because it is the frequency of the magnetic field that sets the limit on how much energy can be transferred between two coils of a given size.
Not everything is ready yet, but the team is working with two companies that manufacture these semiconductors, so that the commercial products meet all the necessary requirements.
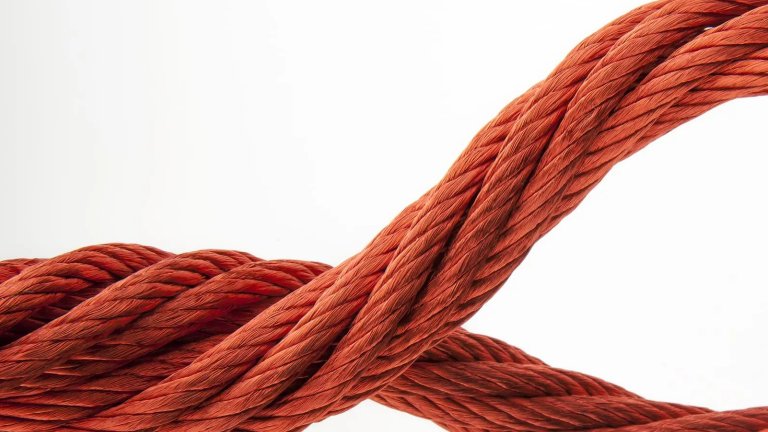
Another recent technological leap involved the copper wires of the coils that send and receive the energy – the transmitting coil creates an oscillating magnetic field that forms the actual bridge for the flow of energy to the receiving coil.
Here too the aim is to use the highest possible frequency. “So it doesn’t work with coils wound with ordinary copper wire, it would lead to very large losses at high frequency,” Liu detailed.
Because of this, traditional copper windings are being replaced by braided “copper ropes”, formed by up to 10,000 very fine copper wires, each measuring between 70 and 100 micrometers in diameter, very similar to strands of hair.
These braids, known as litz wires, adapted for high currents and high frequencies, only reached the market in the last few years – the term litz wire comes from litzendraht, a German term meaning twisted or braided wire.
The team is also taking advantage of state-of-the-art capacitors, which are used to add reactive power, which is a prerequisite for the coil to be able to generate a strong enough magnetic field.
With the first prototypes assembled, the work is now focusing on increasing the set’s efficiency, but the team believes it is close to reaching commercial standards.
What is inductive charging?
Inductive recharging means that electrical current can be transferred over a short distance, whether through air, water or other non-metallic materials, without any contact or wiring.
The principle is the same as that used in induction cookers found in many kitchens: A high-frequency alternating current passes through a coil and produces an oscillating magnetic field.
However, unlike cooking, where the objective is to generate heat, inductive charging presupposes the existence of a second coil on board the vehicle, which captures the energy of the magnetic field and converts it back into electricity. As the magnetic field is oscillating, what comes out are pulses of alternating current, which then goes through a process called rectification, which converts it into direct current that recharges the batteries.
But there is also an unwanted generation of heat, which causes part of the energy to be transferred to be lost. Thus, minimizing heating as much as possible is an important goal for the development of inductive charging technology.